A company needs different types of machinery and systems to produce and provide its products or services to its clients. Every component that takes part in these processes is an important asset, and it should be taken care of. And you could take many approaches to do so, but today we are going to talk about an approach that is ideal when you don’t have enough resources, are operating on some expensive machinery, or even have never applied a maintenance routine before and don’t know where to get started. Risk-Based Maintenance. But what exactly is risk-based maintenance? Let’s find out.
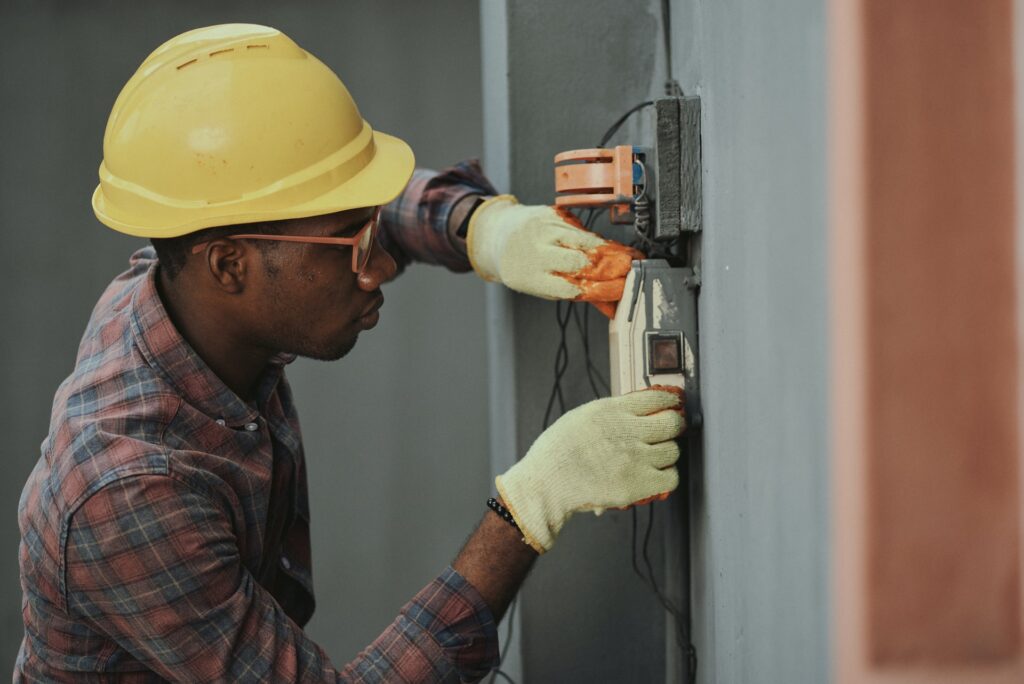
What Is Risk-Based Maintenance?
Risk-based maintenance, or RBM, is designed to provide maintenance in a strategic way. It’s based on the analysis of every machinery and system that is used in the company, in search of the combination between the machinery or system that would have the greatest impact if something happens to it, making it critical for the company’s function. The benefit of this type of maintenance is that it will reduce expenses on reparations and replacement of the company assets while reducing the risk of failure from its components.
This is how it works.
Collecting Data
Your company uses specific machinery and systems to perform its different tasks. Using a measurement system, the person in charge will give a number to each machine or system based on different factors and the likelihood of them needing to be repaired or replaced in the near future. He or she will look at things such as how often every piece of machinery and system is being used, if reparations were needed and how often, the environment and how it affects it, safety, etc.
Risk Evaluation and Consequences
If any of those machines or systems fail for any reason, it will have a smaller or bigger impact on the company. Risk evaluation seeks to determine which have a higher probability of breaking or failing, how frequently it has failed in the past and how regularly it might occur in the future, the conditions and environment in which such machinery or system functions, and if a failure occurs, what is the impact that failure will carry for the company. Not just as the financial losses the company might face, but the safety hazard for employees and even the reputation of the company.
Rank the results
With all the information gathered, now you can determine which machinery and/or systems represent the biggest risk for the company operation and which would have the lowest impact if something should happen to them.
Plan of Action
The idea of risk-based maintenance is to avoid having to repair or replace a machine or system. So, taking into consideration the rank you previously made, you can create an action plan to schedule an inspection, and do maintenance tasks on the machinery and systems that represent a higher risk for the company. The ones that represent low or no risk might have basic maintenance or no maintenance at all for this cycle. And the concept of ‘cycle’ takes us to the next important point.
Repeat The Risk-Based Maintenance Process
Being weekly, monthly, or on another timeframe that suits the need of your company, you should repeat these steps to reevaluate risk and keep your action plan focused on the machines and systems with the highest risk first, and the ones with the lowest risk last. This way, you will make sure that you are always taking care of what is most critical at the moment, and that you are not throwing away valuable resources, such as money and time in machinery and systems that are not in need of maintenance at all.
Should Every Company Have Risk-Based Maintenance?
While it’s true that every company could benefit from risk-based maintenance, some could see a much bigger benefit from it than others.
Small Companies or With Few Pieces of Machinery
If you have a small company or don’t have a replacement in place if a key machine breaks down, then you could see a great benefit from implementing RBM. This maintenance system would help you determine what you need to do to take care of your systems or machines, so you don’t see any losses for an unexpected failure.
Expensive Machinery
If the machinery your company uses to produce its products or offer services costs thousands of dollars and more, replacing them or even repairing them will cost the company a big amount of cash. You could —and should— prevent this by having a risk-based maintenance plan in place.
Companies With Limited Resources
The cost of repairing and replacing machinery tends to be high. But what it’s more important, it can be avoided if you apply risk-based maintenance. True, at some point you still might need to replace a machine or system, but let that happen when it becomes obsolete due to technologies improvements and not because it has failed badly.
How Do Companies Perform Risk-Based Maintenance
There are basically two ways to perform risk-based maintenance:
- With humans, which means that you should either hire a professional and take your personnel from their duties for some time every now and then;
- With a SaaS —Software as a Service—, such as OneView, which will make the process a lot easier, faster, and smoother, avoiding possible mistakes and having everything in one place.
Check out OneView and take one more step to make sure your company stays in business for a long time.
If you have any questions, tap on the bubble on the right, and contact us. We will be more than happy to help.